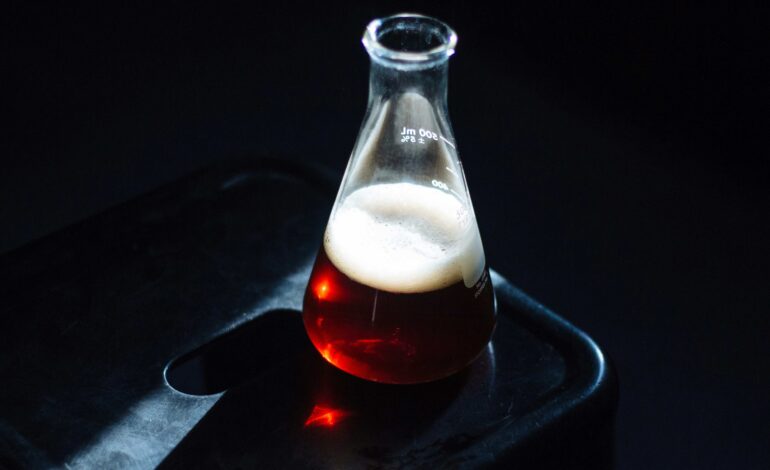
Bunker Fuel Blending Techniques for Optimal Performance
Introduction
Bunker fuel blending is a critical process in the maritime industry, aimed at achieving fuels that meet specific performance, regulatory, and economic requirements. Blending involves combining different grades of fuel oils and additives to enhance fuel properties such as viscosity, density, sulfur content, and stability. This article explores various bunker fuel blending techniques, their importance, methods, challenges, and future trends in the pursuit of optimal fuel performance.
Importance of Bunker Fuel Blending
Bunker fuel, derived from refining crude oil, comes in various grades with differing compositions and properties. Blending allows for customization to meet the precise operational needs of marine engines, ensuring compliance with environmental regulations, improving combustion efficiency, and minimizing maintenance issues. It also optimizes cost-effectiveness by utilizing available fuel resources effectively.
Techniques for Bunker Fuel Blending
1. Gravity Mixing
Method: Gravity mixing involves blending different grades of bunker fuels using tanks or blending lines, relying on the force of gravity to achieve homogeneity.
Advantages:
- Simple and cost-effective method.
- Suitable for blending fuels with similar viscosities.
Challenges:
- Limited precision in achieving specific fuel properties.
- Requires sufficient storage and handling infrastructure.
2. In-line Blending
Method: In-line blending integrates blending components directly within fuel transfer lines using blending pumps and control systems.
Advantages:
- Enables precise control over blend ratios and properties.
- Minimizes the need for additional storage capacity.
Challenges:
- Requires sophisticated blending equipment and control mechanisms.
- Initial setup costs may be high.
3. Component Digital Blending
Method: Component digital blending utilizes advanced software and sensors to precisely meter and blend components in real-time based on predetermined recipes.
Advantages:
- Offers exceptional accuracy and repeatability in blending.
- Enables on-the-fly adjustments to optimize blend properties.
Challenges:
- Dependent on reliable data and calibration for accurate blending.
- Initial investment in digital infrastructure and training.
4. Batch Blending
Method: Batch blending involves pre-mixing components in predetermined quantities before storage or distribution.
Advantages:
- Provides flexibility in blending large quantities of fuel.
- Allows for thorough mixing and quality control.
Challenges:
- Requires dedicated blending facilities and equipment.
- May lead to inventory management challenges.
5. Dynamic Blending
Method: Dynamic blending adjusts blend ratios in response to real-time feedback from fuel quality sensors and engine performance data.
Advantages:
- Optimizes fuel properties based on actual engine requirements.
- Enhances fuel efficiency and engine performance.
Challenges:
- Requires robust data acquisition and processing systems.
- Initial setup and integration with onboard systems can be complex.
Challenges in Bunker Fuel Blending
Achieving optimal bunker fuel blends involves overcoming several challenges, including:
- Quality Control: Ensuring consistent blend quality and adherence to specifications.
- Compatibility: Managing interactions between blend components, additives, and engine systems.
- Regulatory Compliance: Meeting environmental standards for emissions and sulfur content.
- Cost Management: Balancing performance improvements with operational costs.
Future Trends and Innovations
The future of bunker fuel blending is shaped by advancements in technology, sustainability initiatives, and regulatory developments. Key trends include:
- Green Blends: Incorporating biofuels and renewable components to reduce environmental impact.
- AI and Automation: Utilizing artificial intelligence for predictive blending and autonomous operations.
- Smart Blending Systems: Integrating sensors and real-time data analytics for precise control and optimization.
Conclusion
Bunker fuel blending is a pivotal process for optimizing fuel performance in maritime operations, balancing efficiency, compliance, and cost-effectiveness. Techniques such as gravity mixing, in-line blending, digital blending, batch blending, and dynamic blending offer diverse approaches to tailor bunker fuels to meet specific operational needs. As industry demands evolve, the integration of advanced blending technologies and sustainable practices will continue to drive innovation, ensuring that bunker fuels support efficient and environmentally responsible shipping practices worldwide.