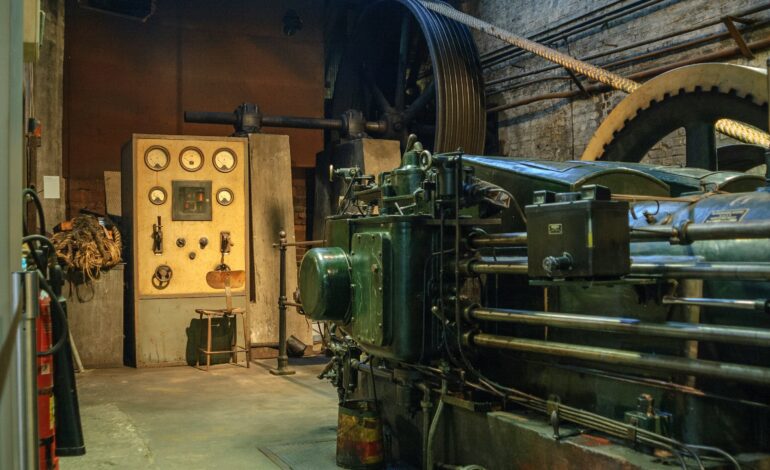
Impact of Bunker Fuel Quality on Marine Engine Wear and Tear
Introduction
The quality of bunker fuel plays a pivotal role in the performance and longevity of marine engines. Variations in fuel quality can significantly impact engine wear and tear, influencing maintenance schedules, operational costs, and overall vessel efficiency. This article examines how bunker fuel quality affects marine engine wear and tear, highlighting key factors and potential solutions to mitigate adverse effects.
Key Factors Influencing Engine Wear and Tear
1. Sulfur Content
High sulfur content in bunker fuel can lead to the formation of sulfuric acid during combustion, which is highly corrosive to engine components. The IMO 2020 regulations, which limit sulfur content in marine fuels to 0.5%, have been introduced to mitigate these effects. However, engines that previously ran on high-sulfur fuels may still experience residual wear and tear from past usage.
2. Cat Fines
Catalytic fines (cat fines) are microscopic, abrasive particles present in residual fuels that originate from refinery processes. These particles can cause significant abrasive wear on engine components, particularly fuel injectors, piston rings, and cylinder liners. High concentrations of cat fines can accelerate wear rates, leading to increased maintenance needs and potential engine failures.
3. Viscosity and Density
Fuel viscosity and density are critical parameters that influence fuel injection and combustion efficiency. Fuels with inappropriate viscosity levels can cause poor atomization, incomplete combustion, and increased deposits on engine components. Additionally, high-density fuels may lead to difficulties in fuel handling and storage, further complicating engine operation and maintenance.
4. Water and Contaminants
The presence of water and other contaminants in bunker fuel can cause significant damage to marine engines. Water can lead to corrosion and microbial growth, while contaminants like dirt and sludge can clog fuel filters and injectors. These issues can result in reduced engine efficiency, increased wear and tear, and higher maintenance costs.
Impact on Engine Components
1. Fuel Injectors
Fuel injectors are particularly susceptible to damage from poor-quality fuel. Cat fines and other contaminants can cause abrasive wear, leading to reduced injection efficiency and fuel atomization. This can result in incomplete combustion, increased fuel consumption, and higher emissions.
2. Piston Rings and Cylinder Liners
Piston rings and cylinder liners are critical components that are directly impacted by fuel quality. High sulfur content can cause acidic corrosion, while cat fines lead to abrasive wear. Poor-quality fuel can also cause increased deposits on these components, reducing their lifespan and performance.
3. Turbochargers
Turbochargers can suffer from fouling and erosion due to poor fuel quality. Incomplete combustion and high levels of contaminants can lead to deposit formation on turbocharger blades, reducing their efficiency and increasing the risk of failure. Regular maintenance and cleaning are necessary to mitigate these effects.
Mitigation Strategies
1. Fuel Quality Management
Implementing stringent fuel quality management practices is essential to mitigate the impact of poor-quality fuel. This includes regular testing and monitoring of fuel properties, such as sulfur content, viscosity, density, and the presence of cat fines and contaminants. Ensuring that bunkered fuel meets specified quality standards can significantly reduce engine wear and tear.
2. Fuel Treatment Systems
Advanced fuel treatment systems, including centrifuges, filters, and chemical additives, can help remove contaminants and improve fuel quality before it enters the engine. These systems are effective in reducing the concentration of cat fines, water, and other impurities, thereby protecting engine components from excessive wear.
3. Engine Maintenance and Monitoring
Regular engine maintenance and monitoring are crucial for early detection and prevention of wear and tear caused by poor fuel quality. Implementing condition-based monitoring systems that track engine performance and component wear can help identify issues before they lead to significant damage. Routine inspections and timely maintenance interventions are vital to maintaining engine health.
4. Lubrication Management
Proper lubrication management is essential to mitigate the effects of poor fuel quality on engine wear and tear. Using high-quality lubricants that provide adequate protection against corrosion, wear, and deposits can extend the lifespan of engine components. Regular monitoring of lubricant condition and replenishing additives as necessary can enhance engine performance and durability.
Conclusion
The quality of bunker fuel has a profound impact on marine engine wear and tear. High sulfur content, cat fines, inappropriate viscosity and density, and the presence of contaminants can all contribute to accelerated wear and increased maintenance requirements. Implementing robust fuel quality management practices, advanced fuel treatment systems, regular engine maintenance, and proper lubrication management are key strategies to mitigate these effects. By addressing the challenges associated with poor-quality fuel, the maritime industry can enhance engine performance, reduce operational costs, and extend the lifespan of critical engine components.