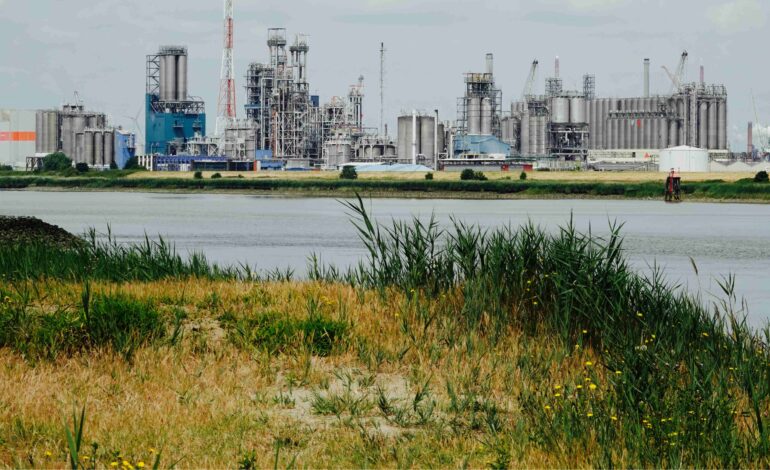
Advanced Materials for Bunker Fuel Storage and Piping Systems
In the dynamic landscape of marine and industrial sectors, the evolution of bunker fuel storage and piping systems is poised for a transformative leap, driven by advancements in materials science. Traditionally, these systems have relied on robust but conventional materials like steel and concrete, which offer durability but often fall short in terms of efficiency, sustainability, and long-term cost-effectiveness. However, the emergence of advanced materials is reshaping these critical infrastructures, promising enhanced performance, environmental benefits, and operational efficiencies.
The Rise of Advanced Materials
The demand for more efficient and sustainable fuel storage solutions has spurred research and development into advanced materials such as fiber-reinforced polymers (FRP), advanced composites, and corrosion-resistant alloys. These materials offer significant advantages over traditional options:
- Lightweight Durability: Unlike steel, which is heavy and prone to corrosion, advanced composites and FRP materials are lightweight yet incredibly strong. This characteristic not only reduces the structural load on vessels and infrastructure but also extends the lifespan of storage tanks and piping systems.
- Corrosion Resistance: Corrosion remains a persistent challenge in marine environments due to saltwater exposure and chemical reactions. Advanced materials like corrosion-resistant alloys and polymer-based composites are engineered to withstand harsh conditions, minimizing maintenance costs and operational downtime.
- Flexibility in Design: The versatility of advanced materials allows for intricate and customized designs that optimize space utilization and installation efficiency. Modular components made from these materials can be prefabricated off-site, reducing construction timelines and on-site disruptions.
- Environmental Sustainability: As global regulations tighten around emissions and environmental impact, advanced materials offer eco-friendly solutions. They can contribute to reducing carbon footprints through improved energy efficiency and lower emissions during production and operation.
Applications and Innovations
In practical terms, these advancements are already making waves across the maritime industry and beyond:
- LNG Bunkering Facilities: LNG (liquefied natural gas) is increasingly favored as a cleaner alternative to traditional bunker fuels. Advanced materials play a crucial role in constructing LNG storage tanks and transfer systems, ensuring safety and efficiency.
- Smart Monitoring and Maintenance: Integrating advanced materials with IoT (Internet of Things) technologies enables real-time monitoring of structural integrity and performance metrics. This proactive approach to maintenance enhances reliability and safety.
- Hybrid Solutions: Combining different advanced materials allows for hybrid solutions that leverage the strengths of each material type. For instance, integrating carbon fiber composites with ceramic coatings enhances both strength and thermal resistance.
Challenges and Future Directions
Despite their promise, adopting advanced materials in bunker fuel storage and piping systems presents challenges such as initial costs and compatibility with existing infrastructure. However, ongoing research focuses on overcoming these hurdles through improved manufacturing techniques, cost-effective production scales, and enhanced material performance.
Looking ahead, the trajectory of advanced materials in bunker fuel storage and piping systems appears poised for continued growth. Innovations in nanotechnology, biocomposites, and 3D printing hold the potential to further revolutionize these critical infrastructures, offering unprecedented levels of efficiency, sustainability, and resilience.
In conclusion, the integration of advanced materials marks a pivotal shift towards a future where bunker fuel storage and piping systems are not only robust and reliable but also sustainable and adaptable to evolving global standards. As industries embrace these innovations, the benefits of enhanced performance and reduced environmental impact will undoubtedly redefine the benchmarks of success in marine and industrial applications.