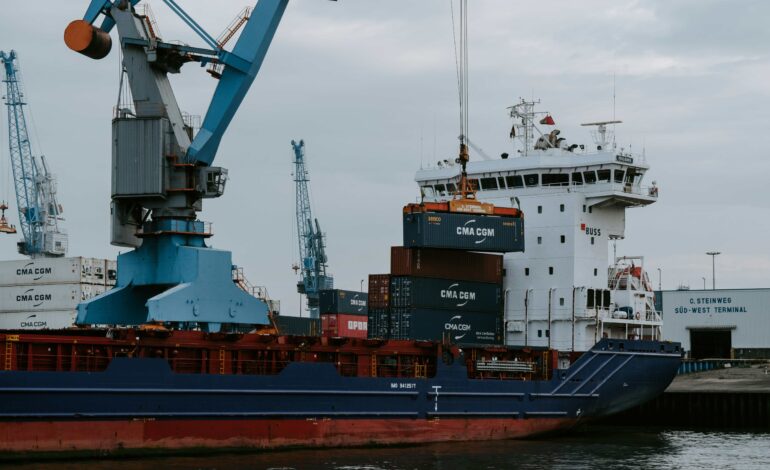
Advances in Predictive Maintenance for Bunker Fuel Systems
Predictive maintenance has become indispensable in enhancing the reliability and efficiency of bunker fuel systems within the maritime sector. By harnessing data analytics, sensor technologies, and predictive algorithms, ship operators can proactively monitor equipment conditions, anticipate potential failures, and optimize maintenance schedules. This article delves into the latest developments in predictive maintenance for bunker fuel systems and their implications for operational performance.
Importance of Predictive Maintenance
Bunker fuel systems are crucial for maritime operations, providing fuel for propulsion and onboard activities. Ensuring these systems operate reliably and efficiently is essential to minimize downtime and maintenance costs. Unlike traditional maintenance approaches that rely on scheduled checks or reactive repairs, predictive maintenance focuses on early detection of issues, thereby preventing failures and optimizing maintenance efforts.
Key Technologies Driving Progress
- Data Analytics and Machine Learning:
- Condition Monitoring: Embedded sensors in bunker fuel systems gather real-time data on parameters like fuel flow, temperatures, pressures, and vibrations.
- Integrated Data Analysis: Advanced analytics platforms merge sensor data with historical maintenance records and operational data to identify patterns and anomalies.
- Machine Learning Algorithms: These algorithms analyze complex datasets, enabling predictive models to forecast equipment failures accurately.
- Remote Monitoring and IoT:
- IoT-enabled Sensors: Internet of Things (IoT) devices facilitate remote monitoring of bunker fuel systems, allowing operators to oversee equipment health from shore or onboard.
- Real-time Alerts: IoT sensors provide immediate alerts for abnormal conditions or potential failures, enabling timely interventions and proactive maintenance.
- Condition-Based Strategies: Continuous monitoring supports condition-based maintenance, where repair schedules are based on actual equipment conditions rather than fixed intervals.
- Digital Twins and Simulation:
- Digital Twin Technology: Digital twins create virtual replicas of bunker fuel systems based on real-time data, enabling simulation of performance scenarios and predictive analysis.
- Predictive Simulation: By simulating various operational conditions, digital twins predict potential failures and optimize operational strategies.
- Performance Optimization: Insights from digital twins aid in optimizing fuel consumption, improving efficiency, and extending equipment lifespan.
Benefits of Predictive Maintenance for Bunker Fuel Systems
- Enhanced Reliability: Early detection of equipment issues reduces the likelihood of unexpected failures, ensuring continuous operation and minimal downtime.
- Cost Efficiency: Predictive maintenance mitigates unplanned repairs and downtime, leading to lower maintenance costs and improved operational efficiency.
- Improved Safety: Proactively addressing equipment failures enhances safety for crew members and reduces risks associated with fuel system malfunctions.
- Optimized Performance: Continuous monitoring and analysis optimize bunker fuel system performance, ensuring efficient fuel usage and compliance with environmental regulations.
Case Studies and Industry Applications
- Large Container Ships: Major shipping companies utilize predictive maintenance to monitor critical components like fuel pumps and valves, ensuring reliability during long voyages.
- Tanker Fleets: Tanker operators leverage predictive analytics to monitor fuel transfer systems, reducing the risk of leakage or contamination during fuel operations.
- Cruise Ships: Cruise lines integrate IoT sensors and digital twins to manage bunker fuel quality and consumption rates, optimizing onboard energy management and reducing environmental impact.
Future Trends and Outlook
- Integration with AI: Advancements in artificial intelligence (AI) will enhance predictive maintenance capabilities, enabling more accurate predictions and automated decision-making.
- Blockchain for Transparency: Blockchain technology may be used to track fuel quality and transactions, ensuring transparency and compliance with regulatory standards.
- Sustainability through Predictive Analytics: Predictive maintenance will play a crucial role in supporting sustainable shipping practices by optimizing fuel efficiency and reducing emissions.
Conclusion
The evolution of predictive maintenance is revolutionizing the management of bunker fuel systems in the maritime industry. By leveraging data-driven insights and innovative technologies, ship operators can achieve higher reliability, lower costs, and improved operational efficiency. As the industry embraces digital transformation and sustainability goals, predictive maintenance remains pivotal in fostering safer, more efficient, and environmentally responsible marine operations.