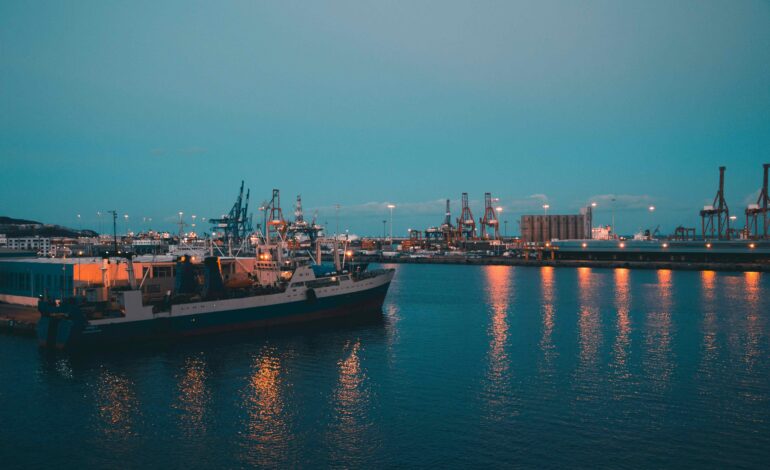
Bunker Fuel Blending: Techniques and Challenges
Bunker fuel blending is a critical process in the maritime industry, involving the mixing of different types and grades of fuel to meet specific performance requirements while optimizing cost-efficiency. This article delves into the techniques used in bunker fuel blending, explores the challenges associated with this practice, and discusses the importance of quality control in ensuring safe and efficient vessel operations.
Techniques of Bunker Fuel Blending
- Component Selection: Blending involves selecting appropriate components of varying viscosity, density, and sulfur content to achieve desired fuel specifications. Components may include heavy fuel oils (HFO), marine gas oils (MGO), and additives.
- Mixing Ratios: Blending ratios are meticulously calculated to achieve the desired viscosity and sulfur content required for compliance with regulatory standards, such as MARPOL Annex VI, which sets limits on sulfur emissions.
- Additive Incorporation: Additives are often used to enhance fuel stability, lubricity, and combustion efficiency. Common additives include cetane improvers, dispersants, and corrosion inhibitors.
- Homogenization Process: Blended fuels undergo a homogenization process to ensure uniformity and stability, preventing stratification and sedimentation during storage and combustion.
Challenges in Bunker Fuel Blending
- Quality Control: Maintaining consistent fuel quality is challenging due to variations in component properties and blending processes. Quality assurance measures, including rigorous testing and analysis, are essential to detect contaminants and ensure compliance with specifications.
- Compatibility Issues: Incompatible fuel components can lead to chemical reactions, sediment formation, and engine performance issues. Compatibility testing is crucial to prevent operational disruptions and mitigate risks of equipment damage.
- Regulatory Compliance: Blended fuels must adhere to stringent regulatory requirements for sulfur content and emissions. Non-compliance can result in penalties, vessel detentions, and reputational damage for ship owners and operators.
- Operational Considerations: Blended fuels may have different combustion characteristics and handling requirements compared to single-grade fuels, necessitating adjustments in engine settings and operational procedures.
Importance of Quality Control
Effective quality control measures are essential in bunker fuel blending to ensure:
- Safety and Reliability: Blended fuels must meet safety standards to prevent engine malfunctions, equipment damage, and operational hazards.
- Environmental Compliance: Compliance with emission regulations ensures minimal environmental impact and adherence to sustainability goals.
- Cost Efficiency: Optimizing blending processes reduces fuel costs while maintaining performance standards, contributing to operational efficiency and profitability.
Future Trends in Bunker Fuel Blending
- Advanced Blending Technologies: Adoption of automated blending systems and real-time monitoring technologies improves accuracy and efficiency in fuel blending operations.
- Sustainability Initiatives: Growing demand for low-sulfur and alternative fuels, such as LNG and biofuels, influences blending practices to meet evolving environmental regulations.
- Digitalization and Analytics: Integration of digital platforms and data analytics enhances predictive maintenance and optimization of blending processes, ensuring consistent fuel quality and operational performance.
Conclusion
Bunker fuel blending is a complex yet essential practice in maritime operations, balancing performance requirements, regulatory compliance, and cost-effectiveness. By employing advanced blending techniques, maintaining rigorous quality control measures, and adapting to regulatory and technological advancements, the maritime industry can navigate the challenges of bunker fuel blending while achieving sustainable and efficient vessel operations.