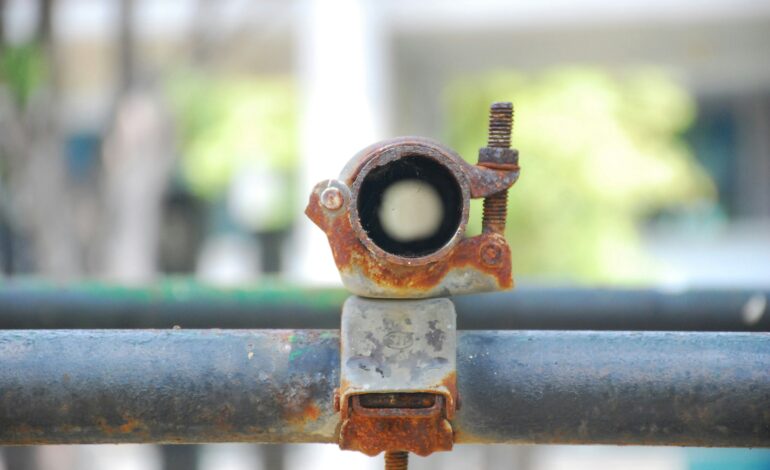
Corrosion Inhibition Strategies in Bunker Fuel Systems
In the realm of maritime and industrial operations, protecting bunker fuel systems from corrosion is essential for maintaining efficiency, prolonging equipment life, and reducing maintenance costs. This article explores various methods of corrosion inhibition, their effectiveness, and their implications for bunker fuel systems.
Understanding Corrosion in Bunker Fuel Systems
- Causes of Corrosion: Bunker fuel systems are vulnerable to corrosion due to factors such as water presence, sulfur content in fuels, acidic combustion by-products, and microbial activity. Corrosion can affect pipelines, storage tanks, fuel pumps, and engine components, leading to operational failures and safety risks.
- Types of Corrosion: Common types include:
- General Corrosion: Uniform deterioration of metal surfaces.
- Pitting Corrosion: Localized damage forming small pits or holes.
- Microbiologically Influenced Corrosion (MIC): Accelerated corrosion due to microbial activity in water-containing environments.
Corrosion Inhibition Strategies
- Chemical Inhibitors:
- Organic Corrosion Inhibitors: Compounds like amines, mercaptans, and phosphates form protective layers on metal surfaces, neutralizing acids or creating barriers against corrosive agents.
- Volatile Corrosion Inhibitors (VCIs): Release vapor-phase inhibitors, creating a protective atmosphere around metal surfaces, even in enclosed spaces.
- Cathodic Protection:
- Impressed Current Systems: Use external power sources to generate a protective electric current, mitigating corrosion on metal surfaces.
- Galvanic Anode Systems: Employ sacrificial anodes made from metals like zinc or aluminum, which corrode first to protect underlying metal structures.
- Coatings and Linings:
- Epoxy Coatings: Applied internally to fuel tanks and pipelines to create barriers against corrosive agents.
- Polyurethane Linings: Provide chemical resistance and durability, extending the life of bunker fuel system components.
- Water Removal and Fuel Treatment:
- Fuel Filtration Systems: Remove water and particulate contaminants from bunker fuels, reducing corrosion risks from water accumulation.
- Fuel Additives: Include additives to enhance fuel stability, inhibit microbial growth, and minimize factors promoting corrosion.
Effectiveness and Implementation Challenges
- Environmental Factors: Inhibitors must be compatible with diverse fuel compositions, operating temperatures, and environmental conditions typical in maritime and industrial settings.
- Maintenance and Monitoring: Regular inspection and maintenance of corrosion protection systems, along with monitoring corrosion rates, are critical for ensuring long-term effectiveness and operational reliability.
Regulatory Compliance and Sustainability
- Environmental Regulations: Compliance with international standards such as IMO fuel quality and sulfur emissions regulations requires corrosion inhibition strategies that align with environmental objectives.
- Sustainable Practices: Adoption of environmentally friendly inhibitors and coatings, coupled with efficient fuel management practices, promotes sustainability by minimizing chemical discharge and environmental impact.
Future Directions
- Advanced Materials and Technologies: Ongoing research focuses on innovative materials, nano-scale inhibitors, and predictive corrosion monitoring technologies to enhance protection and efficiency in bunker fuel systems.
- Industry Collaboration: Collaboration among stakeholders—fuel suppliers, equipment manufacturers, and regulatory bodies—drives innovation and standardization of corrosion inhibition practices across maritime and industrial sectors.
Conclusion
Implementing effective corrosion inhibition strategies is crucial for safeguarding bunker fuel systems, preserving operational efficiency, and supporting sustainability goals. By adopting proactive approaches, leveraging advanced technologies, and adhering to regulatory requirements, stakeholders can mitigate corrosion risks, extend equipment lifespan, and promote environmentally responsible management of bunker fuel systems.