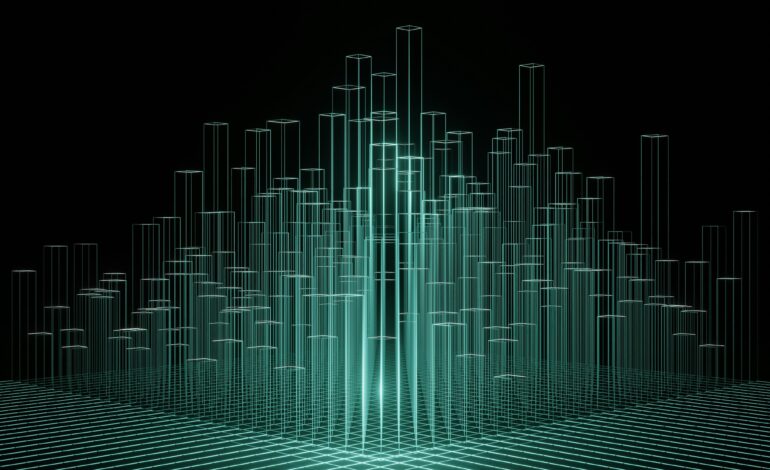
Digitalization and Automation in Bunker Fuel Management
In the maritime industry, where efficiency, compliance, and environmental stewardship are paramount, digitalization and automation have emerged as transformative forces in bunker fuel management. Bunker fuel, which powers the world’s shipping fleet, is now being managed more effectively through advanced technologies that streamline operations, enhance accuracy, and ensure regulatory adherence. This article explores the significant impact of digitalization and automation on bunker fuel management:
- Integrated Monitoring Systems: Digitalization has enabled the integration of sophisticated monitoring systems that track bunker fuel consumption, quality, and emissions in real-time. These systems utilize sensors, IoT devices, and onboard data networks to provide comprehensive insights into fuel usage patterns, allowing ship operators to optimize fuel efficiency and comply with emissions regulations effectively.
- Automated Fuel Quality Assessment: Traditional methods of testing bunker fuel involved manual sampling and laboratory analysis, which could be time-consuming and prone to human error. Automated fuel quality assessment systems now use advanced spectroscopic techniques, such as FTIR and XRF spectroscopy, to analyze fuel composition swiftly and accurately onboard ships. This capability ensures that only compliant fuels are used, minimizing the risk of non-compliance penalties and operational disruptions.
- Predictive Maintenance and Condition Monitoring: Digitalization enables predictive maintenance of ship engines by continuously monitoring engine performance and fuel quality data. Machine learning algorithms analyze historical data to predict equipment failures or performance degradation, allowing preemptive maintenance actions to be taken. This proactive approach reduces downtime, extends equipment lifespan, and optimizes operational efficiency.
- Remote Operations and Decision Support: Remote monitoring and control systems facilitate bunker fuel management from shore-based control centers. Ship operators can remotely monitor fuel levels, consumption rates, and engine performance metrics in real-time, enabling swift decision-making and operational adjustments to maximize fuel efficiency and minimize environmental impact.
- Data Integration and Analytics: The proliferation of digital platforms allows for the seamless integration of bunker fuel data with other operational and logistical systems. Advanced analytics tools process large volumes of data to uncover actionable insights, such as identifying fuel savings opportunities, optimizing route planning based on fuel consumption patterns, and benchmarking performance against industry standards.
- Enhanced Regulatory Compliance: Digitalization supports compliance with stringent environmental regulations, such as MARPOL Annex VI, by ensuring accurate reporting of fuel consumption and emissions data. Automated reporting capabilities streamline regulatory reporting processes, reducing administrative burdens and ensuring transparency in environmental compliance efforts.
- Cybersecurity and Risk Management: As digitalization expands, cybersecurity becomes increasingly critical in protecting sensitive bunker fuel management data from cyber threats. Robust cybersecurity measures, including encryption, network segmentation, and regular vulnerability assessments, are essential to safeguarding digital assets and maintaining operational continuity.
In conclusion, digitalization and automation are revolutionizing bunker fuel management by enhancing operational efficiency, improving regulatory compliance, and advancing environmental sustainability in the maritime industry. As technologies continue to evolve, ship operators and stakeholders are embracing these innovations to navigate the complexities of modern shipping while driving towards a more efficient and environmentally responsible future.