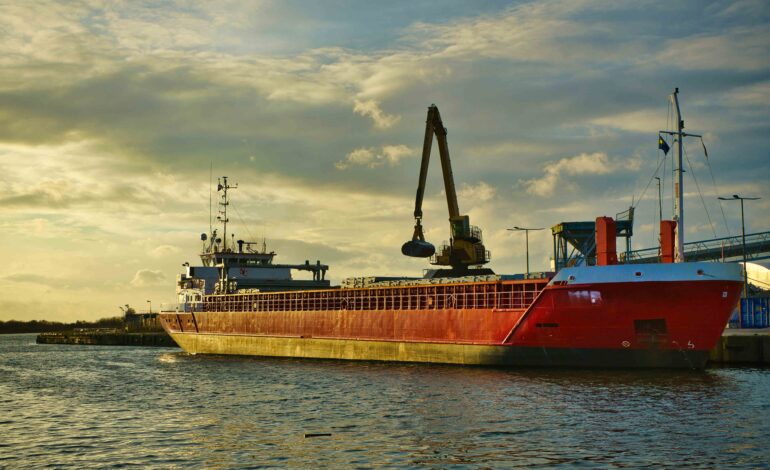
Fuel Injector Technologies for Bunker Fuel in Marine Engines
Introduction
In marine engines, fuel injectors are vital for delivering precise amounts of fuel into combustion chambers at high pressures. This process is crucial for maximizing engine performance, reducing emissions, and meeting strict environmental standards. As the maritime industry evolves, the choice of fuel injectors becomes pivotal. This article explores the different types of fuel injectors used in marine engines with bunker fuels, their benefits, challenges, and future trends.
Types of Fuel Injectors
Main Types:
- Mechanical Unit Injectors (MUI):
- How They Work: Use mechanical force to inject fuel directly into the combustion chamber.
- Application: Common in older or medium-speed marine engines due to their reliability.
- Electronic Unit Injectors (EUI):
- How They Work: Combine electronic controls with mechanical actuators for precise fuel injection timing and quantity.
- Advantages: Improve fuel efficiency, lower emissions, and enhance overall engine performance.
- Common Rail Fuel Injection Systems:
- How They Work: Deliver fuel to injectors at high pressures from a common rail, allowing precise control over injection timing and amount.
- Benefits: Enhance combustion efficiency, reduce noise levels, and support flexible fuel management.
Functions and Benefits
Core Functions:
- Precision Injection: Ensures accurate fuel delivery for optimized combustion, maximizing engine power and efficiency.
- Controlled Timing: Allows precise adjustments in injection timing, improving engine responsiveness and reducing emissions.
- Efficiency Optimization: Facilitates complete fuel combustion, minimizing wastage and improving fuel economy across different operational conditions.
Advantages
- Enhanced Combustion: Improves efficiency, leading to lower fuel consumption and reduced emissions of pollutants like nitrogen oxides (NOx) and particulate matter (PM).
- Increased Durability: Uses advanced materials and designs to extend injector lifespan, lowering maintenance costs and downtime.
- Flexibility: Compatible with various bunker fuels, including heavy fuel oils (HFOs), marine gas oils (MGOs), and low sulfur fuels, ensuring compliance with evolving regulations.
Challenges and Considerations
- Fuel Quality: Variations in fuel composition can affect injector performance, requiring effective filtration and treatment.
- Maintenance: High-pressure injectors need regular upkeep to prevent clogging and ensure peak performance, adding to operational costs.
- Environmental Compliance: Adhering to emission regulations requires precise control over injection parameters to minimize harmful pollutants.
Future Trends
Emerging Developments:
- Dual-Fuel and LNG Compatibility: Advancements in injectors to support dual-fuel engines and liquefied natural gas (LNG) as alternative fuels.
- Digitalization: Integration of sensors and AI for real-time monitoring and optimization of injector performance.
- Material Innovations: Use of ceramics and coatings to enhance durability, efficiency, and resistance to corrosive fuels.
Conclusion
Advanced fuel injector technologies are crucial for improving efficiency and reducing emissions in marine engines using bunker fuels. By enhancing combustion processes and meeting environmental standards, these injectors play a significant role in advancing sustainable marine transportation. As technology evolves and regulations tighten, adopting these innovations will be key to achieving cleaner and more efficient marine operations worldwide.