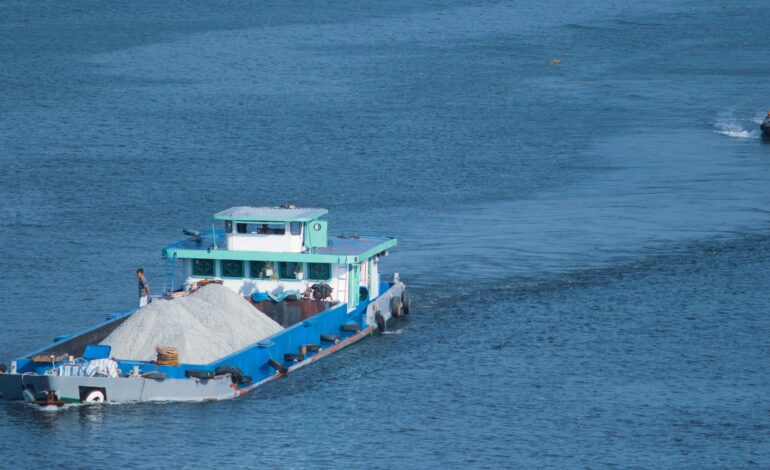
Hydrodynamic Impact of Bunker Fuel Types on Ship Performance
Introduction
The choice of bunker fuel has a significant influence on the overall performance of a ship. Different types of bunker fuels not only affect the engine’s efficiency and emissions but also have a profound impact on the hydrodynamic performance of vessels. This article explores how various bunker fuel types influence ship performance from a hydrodynamic perspective, examining factors such as fuel density, viscosity, and combustion characteristics, and how they interact with ship design and operational parameters.
Types of Bunker Fuels
Residual Fuels
- Heavy Fuel Oil (HFO): A common type of residual fuel, HFO is known for its high viscosity and density.
- Intermediate Fuel Oil (IFO): A blend of heavy fuel oil and marine gas oil, offering intermediate properties.
Distillate Fuels
- Marine Gas Oil (MGO): A lighter, lower viscosity fuel, often used in auxiliary engines and when stricter emission controls are in place.
- Marine Diesel Oil (MDO): A slightly heavier distillate fuel compared to MGO, used in both main and auxiliary engines.
Alternative Fuels
- Liquefied Natural Gas (LNG): A cleaner-burning fuel with different handling and combustion properties.
- Biofuels: Derived from renewable sources, offering varying characteristics based on the feedstock.
Hydrodynamic Factors Influencing Ship Performance
Viscosity and Density
- Fuel Viscosity: High viscosity fuels like HFO require heating to maintain fluidity, impacting fuel handling and injection. Viscosity also influences the lubrication properties of the fuel, affecting engine performance.
- Fuel Density: Heavier fuels can alter the ship’s trim and stability, requiring careful management to maintain optimal hydrodynamic performance.
Combustion Characteristics
- Energy Content: Different fuels have varying energy densities, impacting the amount of fuel needed to produce a certain amount of power.
- Combustion Efficiency: The completeness of fuel combustion affects the generation of thrust and the production of emissions.
Impact on Hull and Propulsion
- Hull Resistance: The type of fuel can influence the fouling rate on the hull, impacting hydrodynamic resistance. Cleaner-burning fuels like LNG tend to result in less soot and particulate deposition.
- Propulsion Efficiency: The quality of fuel combustion directly affects the efficiency of the propulsion system. Poor combustion can lead to increased fuel consumption and reduced thrust.
Analysis of Hydrodynamic Impact by Fuel Type
Heavy Fuel Oil (HFO)
- High Viscosity and Density: Requires heating and specialized handling systems, increasing operational complexity.
- Combustion Characteristics: Produces significant amounts of soot and particulates, contributing to hull fouling and increased resistance.
- Impact on Stability: Heavier fuel can alter the vessel’s center of gravity, affecting stability and requiring careful ballast management.
Marine Gas Oil (MGO)
- Lower Viscosity: Easier to handle and inject, reducing the complexity of fuel systems.
- Cleaner Combustion: Results in less soot and particulate matter, minimizing hull fouling and maintaining better hydrodynamic efficiency.
- Impact on Performance: Generally leads to improved engine performance and reduced maintenance needs.
Liquefied Natural Gas (LNG)
- Combustion Efficiency: High combustion efficiency with minimal particulate emissions, significantly reducing hull fouling.
- Fuel Handling: Requires specialized cryogenic storage and handling systems, impacting vessel design and operational procedures.
- Hydrodynamic Performance: Enhanced performance due to cleaner combustion and reduced fouling, though the need for cryogenic systems can affect ship stability and design.
Biofuels
- Variable Properties: Depending on the feedstock, biofuels can have a wide range of viscosities and densities.
- Combustion Characteristics: Generally produce lower emissions, contributing to reduced hull fouling and better hydrodynamic performance.
- Impact on Operations: The variability in properties requires careful selection and blending to ensure consistent performance.
Practical Considerations and Case Studies
Fuel Management Systems
- Fuel Heating Systems: Necessary for high-viscosity fuels like HFO to ensure proper atomization and combustion.
- Fuel Blending: Used to achieve desired properties and optimize performance. For example, blending HFO with distillates to improve viscosity and combustion characteristics.
Case Study 1: HFO vs. MGO on a Container Ship
- Operational Context: A container ship transitioning from HFO to MGO to comply with emission regulations.
- Observations: Improved combustion efficiency and reduced hull fouling with MGO, leading to better hydrodynamic performance and fuel economy.
- Conclusion: The transition to MGO resulted in lower maintenance costs and improved overall vessel performance.
Case Study 2: LNG Adoption in a LNG Carrier
- Operational Context: A LNG carrier designed to use LNG as its primary fuel.
- Observations: Significant reduction in emissions and hull fouling, resulting in enhanced hydrodynamic efficiency and reduced operational costs.
- Conclusion: LNG offered superior performance characteristics, though initial investment in cryogenic systems was substantial.
Case Study 3: Biofuel Trials on a Bulk Carrier
- Operational Context: Trials of various biofuel blends on a bulk carrier to assess performance.
- Observations: Variability in fuel properties required careful management, but overall emissions were reduced, and hydrodynamic performance was maintained.
- Conclusion: Biofuels demonstrated potential as a cleaner alternative, with the need for further optimization in blending and handling.
Future Trends and Developments
Advanced Fuel Types
- Synthetic Fuels: Development of synthetic fuels from renewable sources to achieve consistent properties and performance.
- Hydrogen: Potential use of hydrogen as a maritime fuel, offering zero emissions and high energy density.
Technological Innovations
- Fuel Treatment Systems: Advanced fuel treatment systems to optimize fuel properties and enhance combustion efficiency.
- Hull Coatings: Development of advanced hull coatings to minimize fouling and maintain hydrodynamic efficiency across different fuel types.
Regulatory and Environmental Considerations
- Emissions Regulations: Ongoing tightening of emissions regulations driving the adoption of cleaner fuels and technologies.
- Sustainability Goals: Increasing focus on sustainability and reducing the environmental impact of maritime operations.
Conclusion
The choice of bunker fuel has a profound impact on the hydrodynamic performance of ships, influencing factors such as fuel handling, combustion efficiency, hull resistance, and overall operational efficiency. Different fuels present unique challenges and benefits, with cleaner-burning fuels like LNG and biofuels offering significant advantages in terms of emissions and hydrodynamic performance. As the maritime industry continues to evolve, the adoption of advanced fuels and technologies will play a critical role in optimizing ship performance, reducing environmental impact, and ensuring regulatory compliance. Understanding the hydrodynamic implications of various bunker fuel types is essential for making informed decisions and achieving sustainable maritime operations.