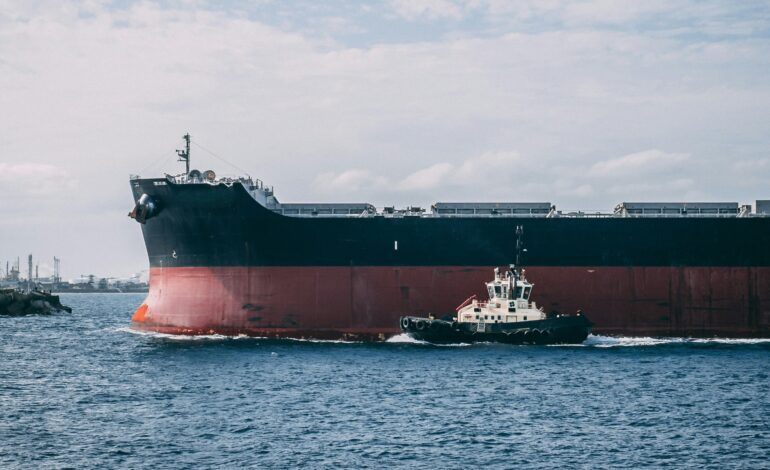
Ship Engine Design Considerations for Different Bunker Fuels
Introduction
Ship engines are critical components in maritime transportation, powering vessels across the world’s oceans. The design and operation of these engines must align with the specific characteristics of bunker fuels used onboard. With various grades available—from heavy fuel oils to cleaner alternatives like marine gas oil and LNG—the choice of bunker fuel significantly influences engine design considerations. This article explores the key factors ship designers and operators must consider when designing engines for different bunker fuels, emphasizing efficiency, emissions control, regulatory compliance, and technological advancements.
Types of Bunker Fuels
Bunker fuels encompass a range of products derived from crude oil refining, each with distinct properties that affect engine performance:
- Heavy Fuel Oils (HFO): Residual fuels with high viscosity and sulfur content, commonly used in large marine engines for their energy density.
- Marine Gas Oil (MGO): Distillate fuels with lower viscosity and sulfur content, preferred for smaller vessels and those operating in regulated emission control areas (ECAs).
- Low Sulfur Fuel Oil (LSFO): Residual fuels with reduced sulfur content (<0.50%), compliant with global sulfur emission regulations.
- Liquefied Natural Gas (LNG): Clean-burning fuel alternative, increasingly adopted for its lower emissions profile and environmental benefits.
Engine Design Considerations
1. Fuel Compatibility and Flexibility
- Fuel Injection Systems: Engine designs must accommodate different fuel viscosities and combustion characteristics, ensuring efficient fuel atomization and combustion stability.
- Material Compatibility: Engines should use materials resistant to corrosion and wear caused by sulfur and other fuel contaminants, especially in HFO applications.
- Dual-Fuel Capability: Engines capable of operating on multiple fuels (e.g., diesel and LNG) provide flexibility to adapt to changing regulatory requirements and fuel availability.
2. Emissions Control
- Exhaust Gas Cleaning Systems (EGCS): Integration of scrubbers and selective catalytic reduction (SCR) systems to reduce sulfur oxides (SOx) and nitrogen oxides (NOx) emissions, ensuring compliance with emission regulations.
- Particulate Filters: Engine designs may incorporate particulate filters to reduce particulate matter (PM) emissions, enhancing air quality and environmental performance.
3. Energy Efficiency
- Combustion Optimization: Engine designs should optimize combustion processes to maximize fuel efficiency and minimize fuel consumption, reducing operational costs and environmental impact.
- Heat Recovery Systems: Utilization of waste heat recovery systems to improve overall thermal efficiency, enhancing energy utilization onboard.
4. Operational Flexibility and Performance
- Load Profile Adaptability: Engines should be capable of adjusting power output and operating efficiently across varying load profiles, optimizing performance under different operational conditions.
- Reliability and Maintenance: Design considerations should prioritize engine reliability and ease of maintenance, minimizing downtime and operational disruptions.
Technological Advancements
Advancements in ship engine technology continue to drive improvements in efficiency, emissions control, and operational flexibility:
- Advanced Control Systems: Integration of smart control systems and predictive maintenance technologies to optimize engine performance and monitor fuel efficiency in real-time.
- Hybrid and Electric Propulsion: Development of hybrid-electric and fully electric propulsion systems for reduced emissions and enhanced operational efficiency.
- Digitalization: Utilization of digital twin technology and data analytics to simulate engine performance, predict maintenance needs, and optimize fuel consumption.
Regulatory Compliance
Global regulations, such as the International Maritime Organization’s (IMO) MARPOL Annex VI, set stringent limits on sulfur and nitrogen oxide emissions from marine fuels. Engine designs must comply with these regulations, influencing fuel selection and emissions control strategies.
Conclusion
Ship engine design for different bunker fuels is a complex and evolving field, balancing efficiency, emissions control, regulatory compliance, and technological advancements. As the maritime industry shifts towards cleaner and more sustainable practices, ship designers and operators must consider fuel flexibility, emissions reduction technologies, and operational efficiency in engine design. By embracing technological innovations and regulatory requirements, stakeholders can foster a future of environmentally responsible shipping while ensuring reliable and efficient maritime transportation worldwide.