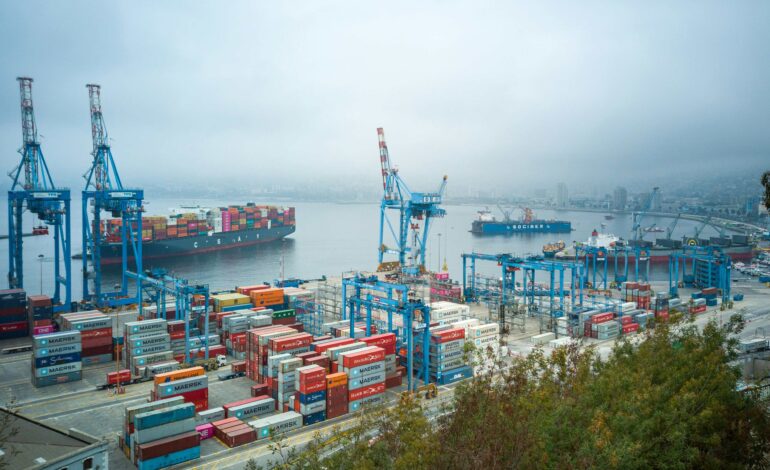
Techniques for Mitigating Bunker Fuel Oxidation and Degradation
Introduction
Bunker fuel oxidation and degradation are significant challenges in the maritime industry, affecting fuel quality, engine performance, and overall operational efficiency. Oxidation and degradation occur due to prolonged storage, exposure to air, and varying temperatures, leading to the formation of sediments, gums, and acids. These issues can cause blockages in fuel systems, corrosion of engine parts, and increased emissions. This article delves into the mechanisms of bunker fuel oxidation and degradation and explores various techniques to mitigate these problems, ensuring optimal fuel quality and performance.
Understanding Bunker Fuel Oxidation and Degradation
Mechanisms of Oxidation
Oxidation is a chemical reaction between bunker fuel and oxygen, leading to the formation of unstable compounds:
- Autoxidation: A self-accelerating process where free radicals react with oxygen, forming peroxides and hydroperoxides.
- Polymerization: Oxidation products can polymerize, forming larger, insoluble molecules that contribute to sediment formation.
Factors Contributing to Degradation
Several factors accelerate the degradation of bunker fuel:
- Temperature: Higher temperatures increase the rate of oxidation reactions.
- Storage Time: Prolonged storage enhances the exposure of fuel to oxygen.
- Contaminants: Presence of water, metals, and other impurities can catalyze degradation reactions.
- Light: UV radiation can initiate oxidation processes in the fuel.
Consequences of Degradation
The degradation of bunker fuel has several adverse effects:
- Sediment Formation: Insoluble particles can clog fuel filters and injectors.
- Acidic Compounds: Formation of acids can corrode fuel systems and engine components.
- Gum Formation: Sticky residues can impair fuel flow and combustion efficiency.
- Increased Emissions: Degraded fuel can lead to higher emissions of pollutants such as particulate matter (PM) and sulfur oxides (SOx).
Techniques for Mitigating Oxidation and Degradation
Fuel Stabilizers and Antioxidants
Adding stabilizers and antioxidants to bunker fuel can significantly reduce oxidation and degradation:
- Antioxidants: Chemicals such as phenols and amines that inhibit free radical formation and propagation.
- Metal Deactivators: Chelating agents that bind with metal ions, preventing them from catalyzing oxidation reactions.
- Stabilizers: Compounds that enhance the overall stability of the fuel by preventing polymerization and sediment formation.
Proper Storage Practices
Implementing proper storage practices is crucial in minimizing fuel degradation:
- Temperature Control: Maintaining consistent, lower temperatures in storage tanks can slow down oxidation reactions.
- Inert Gas Blanketing: Using inert gases like nitrogen to blanket the fuel surface in storage tanks, reducing exposure to oxygen.
- Regular Circulation: Periodically circulating the fuel within the storage tanks to prevent stagnation and stratification.
Fuel Treatment Systems
Advanced fuel treatment systems can effectively manage fuel quality:
- Centrifugal Separators: Devices that remove water, sediments, and impurities from the fuel through high-speed rotation.
- Filtration Systems: Multi-stage filtration systems that capture fine particles and contaminants, ensuring cleaner fuel delivery.
- Coalescers: Systems that aggregate water droplets into larger ones for easier removal, reducing water content in the fuel.
Use of Advanced Materials
Innovative materials can improve the resistance of storage tanks and fuel systems to degradation:
- Corrosion-Resistant Alloys: Using materials like stainless steel and aluminum for storage tanks and pipelines to prevent corrosion.
- Advanced Coatings: Applying protective coatings to the internal surfaces of storage tanks and fuel systems to prevent direct contact between fuel and metal surfaces.
Monitoring and Testing
Regular monitoring and testing of bunker fuel can help detect and mitigate degradation early:
- Spectroscopic Analysis: Techniques like Fourier-transform infrared spectroscopy (FTIR) to identify the presence of oxidation products and contaminants.
- Thermal Analysis: Differential scanning calorimetry (DSC) to assess the thermal stability of the fuel.
- Sediment Tests: ASTM D4870 and other standard tests to measure the sediment content in bunker fuel.
Case Studies and Practical Applications
Case Study 1: Antioxidant Use in Storage Tanks
A major shipping company implemented the use of antioxidants in their fuel storage tanks:
- Result: Significant reduction in sediment formation and improved fuel stability over extended storage periods.
- Conclusion: The use of antioxidants effectively mitigated oxidation, enhancing fuel quality and reducing maintenance costs.
Case Study 2: Inert Gas Blanketing
An oil refinery adopted inert gas blanketing for their bunker fuel storage:
- Result: Oxygen levels in storage tanks were reduced to negligible amounts, slowing down oxidation processes.
- Conclusion: Inert gas blanketing proved to be an effective method for preserving fuel quality during long-term storage.
Case Study 3: Advanced Filtration Systems
A maritime operator installed advanced filtration systems onboard their vessels:
- Result: Improved fuel cleanliness and reduced incidences of clogged filters and injectors.
- Conclusion: Regular filtration of bunker fuel ensured cleaner combustion and better engine performance.
Challenges and Future Directions
Technical and Economic Challenges
Despite the effectiveness of various mitigation techniques, several challenges remain:
- Cost: Implementing advanced systems and additives can be expensive.
- Technical Complexity: Some methods require specialized equipment and expertise.
- Scalability: Adapting techniques for different scales of operation, from small vessels to large fleets, can be challenging.
Research and Development
Ongoing research aims to develop more efficient and cost-effective solutions:
- New Additives: Development of next-generation antioxidants and stabilizers.
- Nano-Coatings: Exploration of nano-coatings for enhanced protection of storage tanks and fuel systems.
- Smart Monitoring Systems: Integration of IoT and AI for real-time monitoring and predictive maintenance of fuel systems.
Conclusion
Mitigating the oxidation and degradation of bunker fuel is essential for maintaining fuel quality, ensuring efficient engine performance, and complying with environmental regulations. Techniques such as the use of stabilizers and antioxidants, proper storage practices, advanced fuel treatment systems, and regular monitoring can significantly reduce the adverse effects of fuel degradation. While challenges remain, ongoing research and technological advancements hold promise for more effective and sustainable solutions in the future. By adopting these strategies, maritime operators can enhance the reliability and longevity of their fuel supplies, contributing to more efficient and environmentally friendly shipping operations.