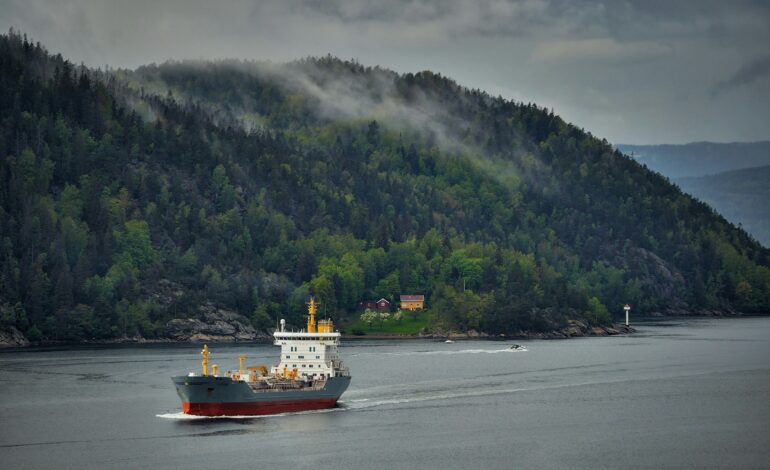
Technological Innovations in Bunker Fuel Heat Exchangers
Introduction
In the maritime industry, heat exchangers are crucial for maintaining bunker fuel systems. These devices are responsible for heating heavy fuel oil (HFO) to the necessary temperature for optimal combustion in marine engines. With increasing environmental regulations and demands for higher efficiency, advancements in heat exchanger technology have become essential. This article explores the latest innovations in this field, focusing on material advancements, design improvements, and enhanced functionalities.
Advanced Materials
1. High-Efficiency Alloys
New high-efficiency alloys have significantly boosted the performance of heat exchangers. These alloys offer excellent thermal conductivity, corrosion resistance, and durability, leading to improved heat transfer and longer service life. Nickel-based alloys, in particular, are popular due to their resilience in high-temperature and corrosive marine environments.
2. Composite Materials
Innovations in composite materials have resulted in the development of heat exchangers that are both lightweight and strong. These composites combine the durability of metals with the corrosion resistance of plastics, creating devices that are more efficient and easier to maintain. This advancement is particularly beneficial for smaller vessels where weight considerations are critical.
Design Improvements
1. Compact Plate Heat Exchangers
Compact plate heat exchangers have become increasingly favored for their high efficiency and space-saving design. These exchangers use a series of thin, corrugated plates to maximize the surface area for heat transfer. Their compact design allows for better space utilization in engine rooms and reduces overall system weight. Additionally, plate heat exchangers are easier to clean and maintain compared to traditional shell-and-tube models.
2. Spiral Heat Exchangers
Spiral heat exchangers feature a unique design that enhances heat transfer efficiency and minimizes fouling. The spiral configuration ensures a continuous flow path, which reduces sediment buildup and maintains consistent heating of bunker fuel. This design is particularly effective for handling viscous fluids like heavy fuel oil, making it ideal for marine applications.
Enhanced Functionalities
1. Intelligent Heat Exchangers
The integration of smart technology into heat exchangers has revolutionized their operation and maintenance. Intelligent heat exchangers equipped with sensors and IoT connectivity allow for real-time monitoring of temperature, pressure, and flow rates. This data can be analyzed to optimize performance, predict maintenance needs, and prevent potential failures. Remote monitoring and adjustment capabilities enhance operational efficiency and reduce downtime.
2. Self-Cleaning Systems
Fouling is a common issue in heat exchangers, especially when dealing with heavy fuel oil. Self-cleaning systems utilize automated mechanisms to remove sediment and deposits from heat exchanger surfaces, maintaining optimal heat transfer efficiency. These systems can employ mechanical scrapers, backflushing, or chemical cleaning agents to keep the heat exchanger clean without manual intervention, reducing maintenance costs and improving reliability.
Environmental and Regulatory Compliance
1. Low-Sulfur Fuel Compatibility
With the IMO 2020 regulations limiting sulfur content in marine fuels to 0.5%, heat exchangers must efficiently handle low-sulfur fuel oils. Innovations in design and materials ensure efficient heating and management of these cleaner fuels. The ability to switch seamlessly between different fuel types is crucial for compliance and operational flexibility.
2. Energy Efficiency and Emissions Reduction
Advancements in heat exchanger technology contribute to overall energy efficiency and emissions reduction in marine engines. Efficient heat exchangers decrease the amount of fuel required to reach optimal operating temperatures, leading to lower fuel consumption and reduced greenhouse gas emissions. These improvements align with global efforts to minimize the environmental impact of the shipping industry.
Conclusion
Innovations in bunker fuel heat exchanger technology are driving significant improvements in efficiency, reliability, and sustainability. Enhanced materials like high-efficiency alloys and composites improve performance and durability. Innovations in design, such as compact plate and spiral heat exchangers, optimize space and heat transfer efficiency. Smart technology and self-cleaning systems reduce maintenance costs and operational downtime. Additionally, these advancements support compliance with environmental regulations and efforts to reduce emissions. As the maritime industry evolves, ongoing research and development in heat exchanger technology will be essential to meet modern shipping demands and environmental goals.