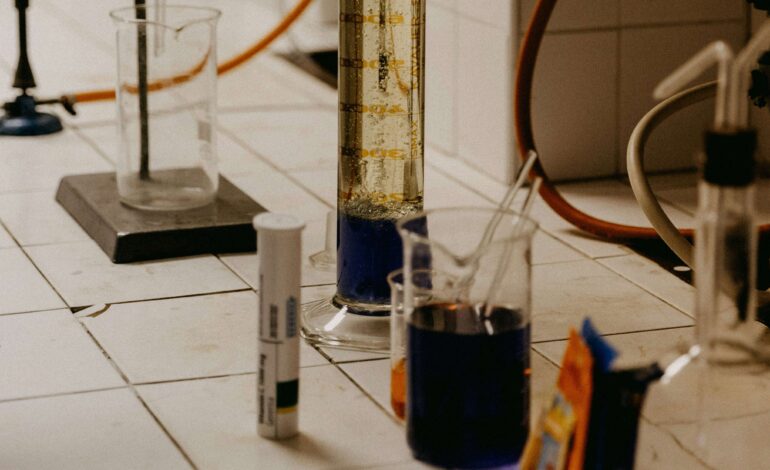
The Chemistry of Bunker Fuels: Composition and Properties
Introduction
Bunker fuels, also known as marine fuels, are the lifeblood of the shipping industry, powering the vast majority of the world’s merchant fleet. Understanding their chemistry is crucial for optimizing their use and minimizing environmental impact. This article delves into the composition and properties of bunker fuels, focusing on the chemical characteristics that define their performance and environmental footprint.
Composition of Bunker Fuels
Bunker fuels are complex mixtures derived from crude oil through the refining process. They are categorized into different grades, primarily distinguished by their viscosity and sulfur content. The two main types are:
- Distillate Marine Fuels (DMF): These are lighter, cleaner fuels similar to diesel. Examples include Marine Gas Oil (MGO) and Marine Diesel Oil (MDO).
- Residual Marine Fuels (RMF): These are heavier, more viscous fuels, often referred to as heavy fuel oils (HFO). They are composed of the residual fractions left after the distillation process.
Key Components:
- Hydrocarbons: The primary constituents of bunker fuels are hydrocarbons, ranging from light paraffins and olefins in distillates to complex aromatic and cyclic structures in residual fuels.
- Sulfur Compounds: Sulfur is a significant component, especially in RMF. It exists in various forms, including hydrogen sulfide (H₂S), mercaptans, thiophenes, and sulfides.
- Nitrogen Compounds: Present in smaller quantities, nitrogen compounds can form during combustion, contributing to NOx emissions.
- Metallic Compounds: Trace metals such as vanadium, nickel, and iron are common in RMF and can cause corrosion and fouling in engines and exhaust systems.
Properties of Bunker Fuels
The properties of bunker fuels are critical in determining their suitability for marine engines and their environmental impact. Key properties include:
- Viscosity: Viscosity is a measure of a fluid’s resistance to flow. RMFs are highly viscous and require heating to reduce viscosity before they can be pumped and burned efficiently. Viscosity affects atomization and combustion efficiency.
- Density: The density of bunker fuels impacts their energy content and combustion characteristics. Higher density fuels generally contain more energy per unit volume but also more impurities.
- Sulfur Content: Sulfur content is a major environmental concern due to its role in forming sulfur oxides (SOx), which contribute to acid rain and respiratory problems. Regulations such as the International Maritime Organization’s (IMO) MARPOL Annex VI limit sulfur content in marine fuels to reduce emissions.
- Calorific Value: The calorific value, or energy content, of bunker fuel determines the amount of energy released during combustion. RMFs typically have a higher calorific value due to their higher carbon content.
- Flash Point: The flash point is the lowest temperature at which a fuel can vaporize to form an ignitable mixture in air. Marine fuels are required to have a minimum flash point of 60°C to ensure safe storage and handling.
- Ash Content: The non-combustible residue left after combustion, known as ash, can cause fouling and damage to engine components. It is more prevalent in RMFs due to higher levels of inorganic impurities.
- Water Content: Water can be present in bunker fuels as a contaminant, leading to corrosion and microbiological growth. It is typically removed through purification processes.
Chemical Reactions During Combustion
The combustion of bunker fuels involves complex chemical reactions that transform hydrocarbons and other components into energy, carbon dioxide (CO₂), water (H₂O), and various pollutants. Key reactions include:
- Complete Combustion: Ideally, hydrocarbons react with oxygen to produce CO₂ and H₂O:𝐶𝑥𝐻𝑦+(𝑥+𝑦4𝑂2)→𝑥𝐶𝑂2+𝑦2𝐻2𝑂CxHy+(O2x+4y)→xCO2+2yH2O
- Incomplete Combustion: In the presence of insufficient oxygen, incomplete combustion occurs, producing carbon monoxide (CO), unburned hydrocarbons (UHCs), and soot (C):𝐶𝑥𝐻𝑦+𝑂2→𝐶𝑂+𝐶+𝑈𝐻𝐶𝑠+𝐻2𝑂CxHy+O2→CO+C+UHCs+H2O
- Sulfur Oxidation: Sulfur in the fuel forms sulfur dioxide (SO₂) and, under certain conditions, sulfur trioxide (SO₃), which can lead to sulfuric acid (H₂SO₄) formation:𝑆+𝑂2→𝑆𝑂2S+O2→SO22𝑆𝑂2+𝑂2→2𝑆𝑂32SO2+O2→2SO3𝑆𝑂3+𝐻2𝑂→𝐻2𝑆𝑂4SO3+H2O→H2SO4
- Nitrogen Oxidation: High combustion temperatures lead to the formation of nitrogen oxides (NOx), which are regulated due to their role in smog and acid rain formation:𝑁2+𝑂2→2𝑁𝑂N2+O2→2NO2𝑁𝑂+𝑂2→2𝑁𝑂22NO+O2→2NO2
Environmental and Operational Challenges
The chemical properties of bunker fuels pose several challenges:
- Emissions: Combustion of high-sulfur RMFs generates significant SOx and particulate matter (PM) emissions. NOx emissions are also a concern, particularly with higher combustion temperatures.
- Engine Wear and Fouling: High levels of ash, metals, and other impurities in RMFs can cause deposits on engine components, leading to increased wear and maintenance costs.
- Regulatory Compliance: IMO regulations, such as the 2020 global sulfur cap, mandate the use of low-sulfur fuels or the installation of exhaust gas cleaning systems (scrubbers) to reduce emissions. Compliance requires careful fuel selection and management.
Advances and Alternatives
To address the environmental impact and operational challenges of traditional bunker fuels, several advancements and alternatives are being explored:
- Cleaner Fuels: Low-sulfur fuels, such as ultra-low sulfur fuel oil (ULSFO) and liquefied natural gas (LNG), produce fewer emissions and are gaining popularity.
- Biofuels: Bio-derived fuels offer a renewable alternative with the potential to reduce greenhouse gas emissions. They can be blended with conventional bunker fuels or used independently.
- Synthetic Fuels: Produced from renewable energy sources, synthetic fuels aim to provide a carbon-neutral alternative to traditional marine fuels.
- Emission Control Technologies: Scrubbers and selective catalytic reduction (SCR) systems help reduce SOx and NOx emissions from existing engines.
Conclusion
The chemistry of bunker fuels is integral to their performance and environmental impact. Understanding the composition and properties of these complex mixtures enables the shipping industry to optimize fuel use, comply with regulations, and explore cleaner alternatives. As the industry evolves, advancements in fuel technology and emission control will play a crucial role in reducing the environmental footprint of marine transportation.