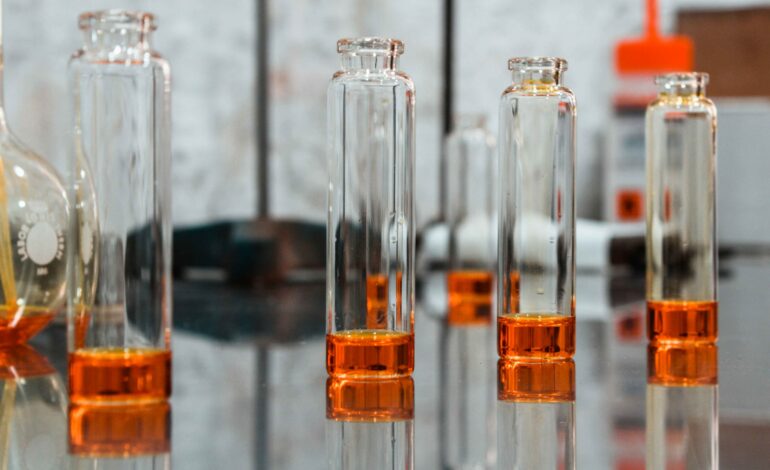
The Chemistry of Bunker Fuels: Composition, Characteristics, and Variability
Introduction:
Bunker fuels, the indispensable energy source for maritime transportation, are intricate concoctions of hydrocarbons derived from crude oil. Their chemistry, marked by a diverse array of compounds and properties, dictates not only the efficiency and performance of marine engines but also their environmental impact. This comprehensive exploration delves into the nuanced chemistry of bunker fuels, elucidating their composition, characteristics, and variability, and underscores their pivotal role in the maritime industry’s quest for sustainability and efficiency.
Composition of Bunker Fuels:
Bunker fuels primarily consist of hydrocarbons, ranging from simple alkanes to complex aromatic compounds, obtained through the refining of crude oil. The refining process, known as fractional distillation, separates crude oil into fractions based on their boiling points, yielding various distillates and residues. Heavy fuel oil (HFO), a residual product, contains long-chain hydrocarbons and high levels of impurities such as sulfur, nitrogen, and metals, making it less refined but economically advantageous. In contrast, marine gas oil (MGO), derived from distillation, exhibits lower viscosity, density, and sulfur content, rendering it cleaner and more suitable for stringent environmental regulations.
Characteristics of Bunker Fuels:
The characteristics of bunker fuels encompass a plethora of parameters, each playing a critical role in their performance and applicability. Viscosity, a measure of a fluid’s resistance to flow, influences fuel injection, atomization, and combustion processes within marine engines. High-viscosity fuels require preheating to facilitate handling and combustion, whereas low-viscosity fuels enhance atomization and promote efficient combustion. Density, another crucial property, affects fuel volume requirements, storage capacities, and transportation logistics. The density of bunker fuels varies with temperature and pressure, necessitating standardized testing methods and correction factors for accurate measurements.
Sulfur content stands as a pivotal characteristic, especially in light of increasingly stringent environmental regulations targeting sulfur oxides (SOx) emissions from maritime activities. Traditional bunker fuels, particularly HFO, have historically contained high sulfur levels, contributing significantly to air pollution and acid rain. To mitigate environmental impact, regulatory bodies such as the International Maritime Organization (IMO) have implemented sulfur emissions control areas (SECAs) and sulfur content limits, culminating in the landmark IMO 2020 regulation mandating a global sulfur cap of 0.5%. This paradigm shift towards low-sulfur bunker fuels has spurred technological innovations and infrastructural investments in sulfur removal technologies, catalytic converters, and alternative fuel formulations.
Variability of Bunker Fuels:
The variability of bunker fuels stems from a myriad of factors, including geographical location, crude oil composition, refining processes, blending practices, and regulatory requirements. Geopolitical tensions, market dynamics, and supply chain disruptions further compound the intricacies of bunker fuel procurement and distribution. Regional disparities in crude oil quality and availability necessitate tailored refining processes and blending strategies to meet local demand and regulatory standards. The blending of additives such as pour point depressants, cetane improvers, and lubricity enhancers augments fuel performance and addresses specific operational challenges, ranging from cold weather operability to engine wear and tear.
Regulatory frameworks exert significant influence on bunker fuel composition and availability, catalyzing industry-wide initiatives towards cleaner and more sustainable fuel options. Emerging technologies such as liquefied natural gas (LNG), biofuels, and hydrogen fuel cells offer promising alternatives to conventional bunker fuels, promising reduced emissions and enhanced environmental stewardship. However, widespread adoption and infrastructure development remain contingent upon economic viability, regulatory support, and technological advancements.
Conclusion:
The chemistry of bunker fuels embodies a dynamic interplay of composition, characteristics, and variability, shaping the trajectory of maritime transportation and environmental sustainability. As the maritime industry confronts evolving regulatory landscapes, technological disruptions, and societal expectations, a nuanced understanding of bunker fuel chemistry is indispensable for navigating challenges and seizing opportunities. By embracing innovation, collaboration, and responsible stewardship, stakeholders can chart a course towards a greener, safer, and more resilient maritime future.