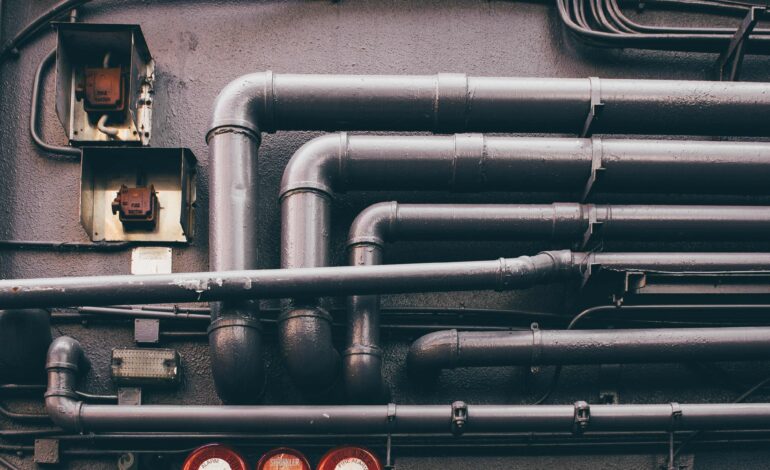
Thermo-Fluid Dynamics of Bunker Fuel Injection Systems
Understanding the thermo-fluid dynamics of bunker fuel injection systems is essential for optimizing combustion efficiency, enhancing fuel economy, and reducing emissions in maritime and industrial applications. This article delves into the intricate processes governing bunker fuel injection, exploring thermal dynamics, fluid mechanics, and their combined impact on system performance.
Fundamentals of Bunker Fuel Injection Systems
Bunker fuel injection systems are integral to the operation of diesel engines in ships and industrial power plants. These systems involve the precise delivery of bunker fuel—typically heavy fuel oil (HFO) or marine diesel oil (MDO)—into combustion chambers where it mixes with air and undergoes combustion. The thermo-fluid dynamics of these systems encompass several key aspects:
- Fuel Atomization and Spraying:
- Atomization Process: As bunker fuel enters the injection system, it undergoes atomization—a process where the liquid fuel is broken down into small droplets. This increases the surface area exposed to oxygen in the combustion chamber, promoting efficient combustion.
- Spray Characteristics: The spray pattern, droplet size distribution, and spray penetration depth influence combustion stability, fuel-air mixing, and overall engine performance.
- Heat Transfer and Combustion:
- Heat Release: Upon ignition, the atomized bunker fuel undergoes rapid combustion, releasing heat energy that drives the engine’s piston or turbine. The efficiency of heat transfer from combustion gases to engine components affects overall system efficiency and thermal management.
- Temperature Distribution: Understanding temperature gradients within the combustion chamber is crucial for preventing thermal stress on engine components and optimizing fuel combustion.
- Fluid Dynamics in Fuel Injection:
- Fuel Flow Characteristics: Fluid dynamics govern the flow of bunker fuel through injection nozzles, pipes, and valves. Factors such as pressure drop, flow rate, viscosity, and turbulence affect the efficiency of fuel delivery and atomization.
- Cavitation and Flow Instabilities: High-pressure conditions within injection systems can lead to cavitation—a phenomenon where vapor bubbles form and collapse, potentially causing erosion and damage to system components.
Optimization Strategies and Challenges
- Injector Design and Optimization:
- Nozzle Geometry: The design of injection nozzles influences fuel atomization and spray characteristics. Optimizing nozzle geometry, hole size, and spray cone angle enhances fuel-air mixing and combustion efficiency.
- Injection Timing: Precise control of injection timing ensures optimal fuel delivery relative to engine load and speed, maximizing power output and minimizing emissions.
- Fuel Quality and Compatibility:
- Viscosity and Temperature: Bunker fuels exhibit varying viscosity with temperature changes. Maintaining proper fuel heating and viscosity control ensures consistent flow characteristics and prevents operational issues related to fuel injection.
- Environmental and Regulatory Considerations:
- Emissions Control: Thermo-fluid dynamics play a crucial role in controlling emissions of nitrogen oxides (NOx), sulfur oxides (SOx), particulate matter, and greenhouse gases. Advanced injection systems and combustion strategies help meet stringent environmental regulations.
- Advanced Technologies and Future Trends:
- Dual-Fuel and LNG Systems: Integration of liquefied natural gas (LNG) and dual-fuel injection systems offers cleaner combustion options, reducing emissions and enhancing fuel flexibility.
- Digitalization and Simulation: Adoption of computational fluid dynamics (CFD) simulations and real-time monitoring systems optimize injector performance, predict system behavior, and facilitate predictive maintenance.
Conclusion
The thermo-fluid dynamics of bunker fuel injection systems represent a critical area of study for improving engine efficiency, reducing environmental impact, and enhancing operational reliability in maritime and industrial applications. By advancing our understanding of fuel atomization, combustion dynamics, and fluid flow within injection systems, engineers and researchers can develop innovative solutions to meet evolving regulatory standards and sustainability goals in the global energy landscape.